Digitalisation
In 2023, FESCO rolled out an extensive array of digitalisation initiatives, unlocking new opportunities for business development.
Our principal digitalisation challenges centred around maintaining FESCO's operational continuity amidst import substitution hurdles. Concurrently, we advanced projects set to build new logistics solutions and information systems. We also pursued innovative ventures as part of Data Office, a dedicated area we focus our efforts on.
FESCO's IT units now comprise a 280‑strong workforce, with key expertise hubs in Moscow and Vladivostok and local offices across over 17 Russian cities. We are setting up competence and business support centres in FSU nations (Kazakhstan, Uzbekistan, Belarus) and in our offices overseas.
Collectively, these IT units manage and support upwards of 80 information systems for FESCO Group's over 6.5 thousand employees.
Guided by our digital strategy in effect, in the forthcoming years we will focus on the priority digitalisation areas below:
- critical information infrastructure and no reliance on imports
- digital business continuity
- digital architecture upgrades
- ongoing evolution into a digital freight forwarding business
- cybersecurity
Customer’s personal account
MY.FESCO customer’s personal account is a self‑service portal for our customers.
Improvement of this service is the key priority of FESCO digitalisation. The main objective of the project is to provide a fully digital transportation service. Our efforts on portal improvement enabled us to implement one of the best and most feature‑rich solutions in the market.
Priority areas of personal account improvement in 2023:
- Dalreftrans personal account launched
- contractual work (expanding the scope of electronic workflow operators for contract signing, entering into contracts with non‑residents) continued
- export and import tracking systems for port‑to‑port shipments enhanced
- coverage of digitisation of door‑to‑door delivery calculations using a map location expanded
- routes as part of the approval protocol for dangerous goods transportation extended
- an APIApplication Programming Interface. suite for seamless customer system integration implemented
- a general cargo calculator for domestic shipments designed
The personal account was piloted in 2017 and back then only supported requests for intermodal imports from Southeast Asia to Vladivostok and Moscow. Today, the service can be used to request any of FESCO’s key transportation services.
In 2023, the growth of orders placed via the personal account continued:
- the number of orders placed via personal accounts increased by 12.5%
- TEU equivalent of orders via personal accounts grew by 22% YoY
- over 2.8 thousand contracts were made via the personal account during the year
Currently, a record 7.5+ thousand users visit MY.FESCO.com every day.
The MY.FESCO services are mainly used to:
- submit and repeat requests for container transportation
- track the shipping and customs status
- download scans of accounting and transportation documents without contacting managers or requesting the documents by mail or phone
- check whether the dangerous goods can be transported along import/transit routes
- conclude contracts
- check if dangerous goods can be transported
- file for customs transit clearance
FESCO also works to develop the following additional services for customers:
- reconcile overpayments
- request and approve reconciliation reports
- control user access for their company
- request a system for securing dangerous or non‑dangerous cargo inside the container
- provide feedback on service quality
Production systems
In 2023, FESCO continued to focus on the development of production systems.
FESCO INTEGRATED TRANSPORT
The year 2022 saw the initiation of a project series to overhaul the production system of FESCO Integrated Transport (FIT), introducing interlinked functional modules within a unified microservice architecture based on the 1C:Enterprise 8 platform.
By 2023, within the FMS. Transportation Management initiative, a component of this project suite, we rolled out the core production module, which automates the end‑to‑end business process of managing, planning, and executing transportation orders. It also encompasses mutual settlements and management reporting as part of the process.
The overarching goal is to supplant the existing production system. While building the solution, aside from automation, we streamlined business processes in place for execution within the system, with a modern domestic technology platform both enhancing the efficiency of key operations and mitigating sanctions risks.
Throughout 2023, the project's architecture was designed, establishing object and module interconnections, core functionalities were developed, and integrations were carried out with other information systems of the Group and key partners. The system's viability and the accuracy of its functionalities were validated by successful functional tests involving prospective users. Commercial deployment is slated for 2024.
These modules fit the overall FMS programme's concept, boasting a cohesive architecture and business process framework. This enables smooth integration with other FMS programme products and FESCO's overall IT infrastructure.
Several system's components were put into commercial operation in 2023:
- transportation of dangerous goods, including preliminary coordination with all parties involved in transportation
- document control – accounting for container expenses
- container repair – a web portal to arrange for container repairs at terminals and depots, enabling selection of the best supplier based on repair time, cost, and quality
- cost control operations – collection and recognition of direct transportation costs, enabling the calculation of the actual cost and profit margin of transportation services
Dalreftrans
In 2023, special attention was paid to one of FESCO's key assets, Dalreftrans, its development and digitalisation of its operations. During the year, digitalisation solutions for the company’s business processes were substantially redesigned:
- the customer’s personal account added e‑commerce features for refrigerated transportation
- rate‑setting features were rearranged, simplified and scaled up
- tracking of containers by rail and sea was introduced
- controls were put in place, reducing human factor potentially affecting data accuracy and timeliness
Dalreftrans became an integral part of FESCO’s digital ecosystem, and its customers can now use the information service according to the common standards of the Company.
The development of Dalreftrans’ production system coincided with strong operating results, which in turn contributed to the company’s growth and an increase in customer demand. In 2023, FESCO recorded a notable uptick in customer engagement compared to 2022:
- a 36% rise in customer transportation orders
- a 25% increase in the customer base
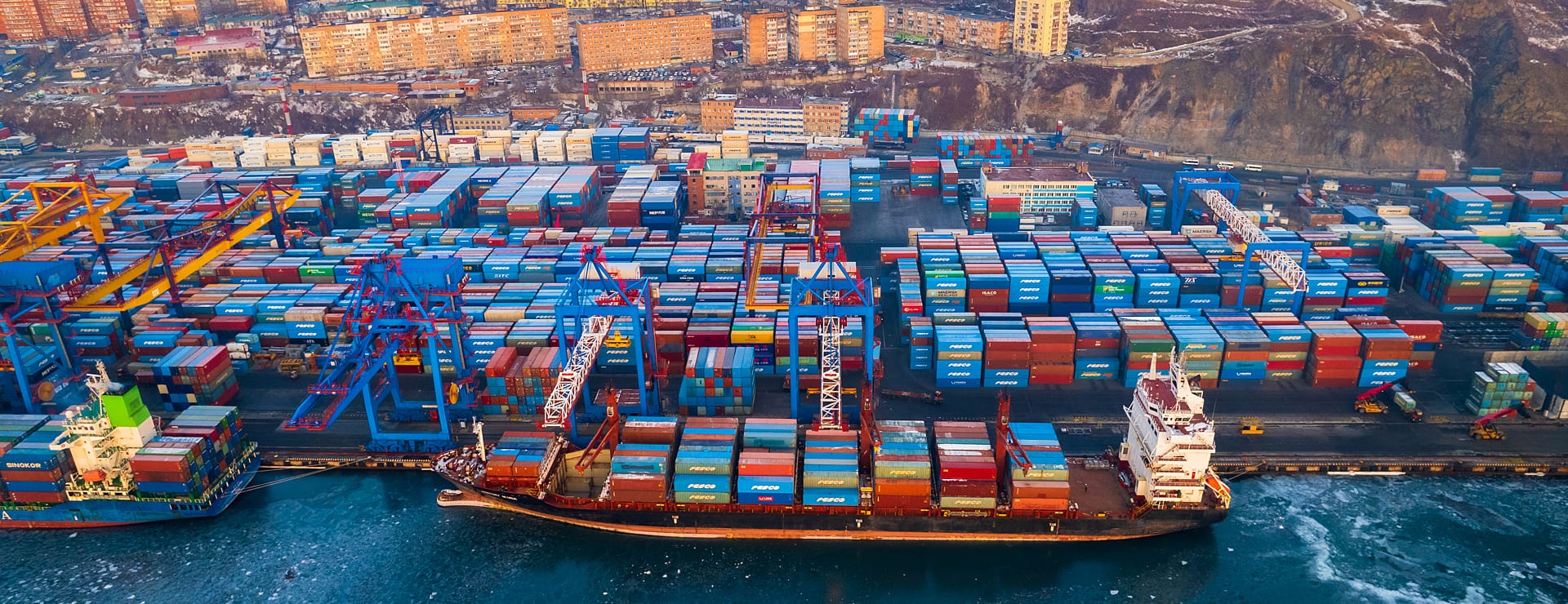
VMTP
FESCO invests considerable effort in rolling out IT solutions that streamline VMTP’s internal processes. In 2023, industry professionals at the Digital Transportation forum acknowledged the achievements of VMTP's port management system, honouring it with awards in the Best Digital Transformation and Digital Leader of the Year categories.
VMTP introduced Russia's first integrated one‑stop‑shop system for regulators – the Federal Customs Service, Russian Railways, and the Federal Service for the Oversight of Consumer Protection and Welfare (Rospotrebnadzor). This development has dramatically accelerated document processing and cargo release from the port by an average of 16‑fold and simplified procedures for the staff of all involved federal agencies. VMTP's digitalisation drive focuses on expediting cargo handling and reinforcing its dominance in Russia in this domain.
Key highlights:
- slashing the export order processing time from 10 hours to just two. In 2023, a staggering 90% of orders at VMTP were placed via its information system and filed to the Federal Customs Service using electronic workflow channels
- reducing customs authorisation times from 48 hours down to three
- cutting time needed for inspections and container weighing by three times
- increasing export container turnaround by 1.5 times and reducing average storage to 13.2 days from the previous year's 19.8
The Mobile Yantar project was completed, integrating a unified radiation control system across the entire VMTP area and introducing a mobile solution for the customs. It can change status of the customs control activities and grants real‑time access to cargo history and customs declarations.
Key highlights:
- eliminating the need for a tally clerk on each radiation control location to register events of alarm going off
- freeing up warehouse space by dismantling stationary radiation survey instruments
- minimising human contact and relieving the workload for the customs staff
In 2023, VMTP took a leap forward by automating its LCL cargo storage warehouse and adopting bin location storage. LCL cargo handling intensity grew by 1.5 times.
The first phase of the Smart and Safe Port initiative wrapped up at the end of the year. We launched video analytics that can automatically detect silhouettes, biometrics, and hazardous zones. We can thus automate processes and mitigate occupational and transportation safety risks. The Company completed piloting the second phase, which will continue into 2024. The project helped set up oversight of loading and unloading operations. This includes AI‑powered automatic identification of container numbers and damage received, along with cargo pinpointing and automatic location of loading/unloading place.
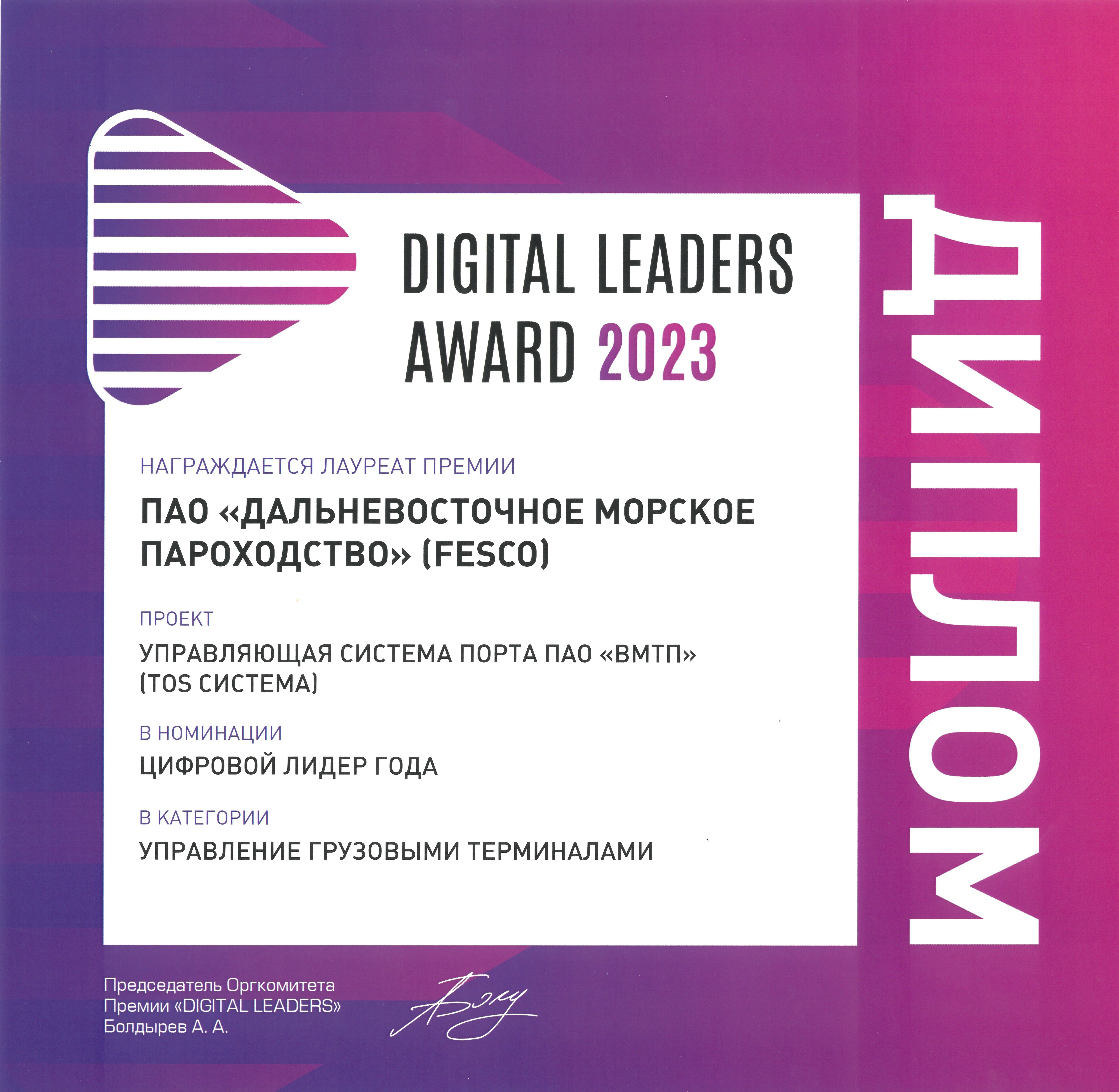
.png)
Automation of manufacturing companies in Kazakhstan
The Company’s growth and launch of new businesses revealed the need to automate activities of the new companies in a quick and efficient manner. FESCO opted for proprietary IT solutions already implemented in the Group. This helped to bring down automation time and offer solutions factoring into the specifics and requirements of the companies. In 2023, these solutions served as the basis for the following companies:
- FESCO Dostyk Limited:
- dispatch of containers from China with transhipment in Kazakhstan
- automated tracking of container location along the entire journey from China to the destination stations in Russia
- FESCO Central Asia – organisation of multimodal container transportation to/from Kazakhstan
Data Office
In 2023, FESCO created Data Office, a fruit of joint effort of business analysts and data engineers, which comprises:
- cutting‑edge analytics and machine learning (ML) capabilities
- a secure reference data warehouse for the Group’s data
- oversight of data reliability and integrity across all systems
- agile BI tools, business glossaries, and regulatory and reference data management
- a key event monitoring and notification system
An enterprise data platform was established, with services configured for an isolated development and monitoring environment. We also designed a target data architecture for analytics in order to scale it up and manage its complexity amidst burgeoning data volumes and variety.
In the realm of BI, analytics, and AI, we did the following:
- initiated major projects to develop reporting within a unified domain‑focused architecture, which enables standardising analytical reporting and enhancing its accessibility
- deployed a new Russian BI system, started migrating analytical reports to domestic software
- piloted ML‑based forecasting for VMTP staff shifts, identifying potential enhancements in freight turnover per container up to 14%
- are running a project to optimise cargo placement at the port
- initiated an HR initiative focused on talent acquisition and onboarding
FESCO asset map
An interactive FESCO asset map has been developed, offering a live view of the Group's assets: position of trains, vessels, and vehicles alongside location of branches and terminals. Users can also connect to terminal cameras in real time.
DIGITAL SERVICES FOR FESCO EMPLOYEES
In 2023, FESCO triumphantly accomplished a transition to HR electronic workflow for its employees.
Key factors that facilitated a swift rollout included:
- commitment to the existing IT infrastructure
- full project management by IT personnel
- high level of HR service automation from the outset
We decided to integrate an external service, providing a digital signature platform for HR documentation, into our existing IT landscape. The organisational scope covered staffed companies, while the functional perimeter embraced nearly all HR documents, exceeding 95%.
FESCO IT steered all project workstreams – legal, methodology, security, and software development. The project was resource‑efficient, largely due to the initially high degree of HR service automation.
Project outcomes:
- 26 FESCO companies moved to electronic workflow covering the employer‑employee relationship
- over 80% of employees digitally sign documents, inclusive of blue‑collar staff
- number of paper documents dropped by more than 40 thousand
- over ten new HR services were launched, with some accessible through a Telegram chatbot
- time and effort required to sign HR documents declined
- standards and processes for handling queries from personnel, including from business units, were aligned
- Anti‑sanctions measures
In 2023, due to the international context, FESCO continued efforts to counteract sanctions along with infrastructure projects. Based on the solutions we tested earlier, a handful of projects were completed to mitigate sanctions risks:
- migration of all FESCO email to a Russian cloud service was completed
- a Russian data centre‑based cloud portal went live, ensuring data transfer for units, with intact access rights
- a Russian video conferencing system was seamlessly integrated
- Russian equipment for reliable front office functioning was purchased and rolled out
- a print service from a domestic manufacturer was implemented to monitor office equipment and enable secure print jobs initiated by employee passes
- a total of 400 Russian‑made laptops were purchased and put into operation
These solutions secure the Company's stable operation in today’s environment
- Under another project, VMTP's wheeled vehicle fleet was outfitted with equipment enabling unified connectivity for all production‑related IT devices
- FESCO’s IT Infrastructure upgrade and fleet IT support
- Import substitution
In 2023, FESCO devised a strategy to implement the import substitution programme. The Company selected a contractor and drafted agreements, whereby FESCO will be audited in a range of areas and a roadmap will be developed. Efforts include piloting projects in these areas:
- IT infrastructure
- information security (infrastructure)
- system software
- standard automated workplace (office software)
- automated process control systems for engineering networks
- telecommunication systems
- business applications
- Development of branches and offices
FESCO is vigorously expanding, not only by establishing new offices but also by revamping existing ones:
- new branches were inaugurated in Yekaterinburg and Kaliningrad
- networks in Novosibirsk and Vladivostok were upgraded
- FESCO actively developed, maintained and upgraded equipment while also creating new jobs. In 2023, nearly 1 thousand workplaces were set up and over 150 thousand queries to technical support service regarding infrastructure and information systems were processed
With an eye on bolstering competitive edges and advancing fleet digitalisation, FESCO initiated an IT infrastructure upgrade and fleet support project. Accomplishments to date:
- IT audits of 27 vessels were completed. Based on their findings, we drafted technical specifications for a contractor to construct or upgrade the structured cable systems network depending on its current state
- state‑of‑the‑art network hardware and user PCs were procured
- fleet‑wide access to the corporate ServiceDesk system was set up, ensuring prompt support for IT‑related crew queries
- efforts to provide the entire fleet with high‑speed coastal (up to 50 km range) 4G‑multirouter internet access and unlimited VSAT satellite internet access are about to finish
- regular IT auditing process in line with vessel service port visits was established
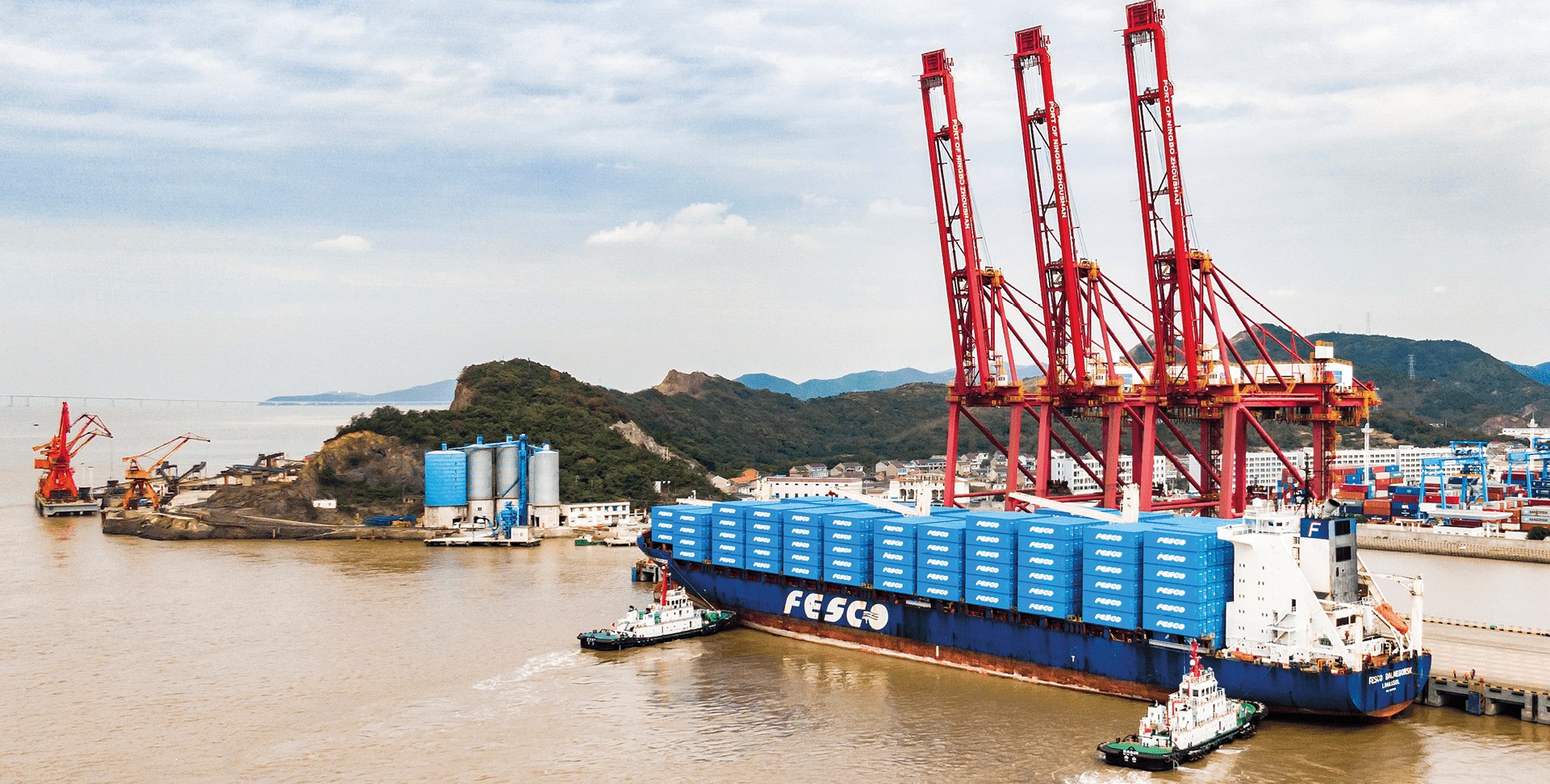
The escalating global geopolitical tensions in 2023 brought about an uptick in cyber threats across the digital domain.
Many Russian companies faced a surge in large‑scale cyberattacks. FESCO's information systems were not immune, witnessing a 1.5‑fold increase in network attacks and a tripling of malware infection attempts YoY.
In response to heightened cyber risks, FESCO is reinforcing its corporate network and refining processes to detect and patch IT infrastructure vulnerabilities.
The year saw a rigorous examination of personal data security processes within our information systems and an appraisal of the effectiveness of existing protective measures. We also conducted penetration tests, simulating intrusion into our corporate network. Our cybersecurity arsenal expanded to include robust tools such as a vulnerability scanner for identifying perimeter threats, enhanced safeguards against illegitimate access to the corporate email system, and mechanisms to prohibit unsafe passwords. These measures significantly enhance the protection of information infrastructure from malicious attacks, reducing the risks of destructive effect on FESCO’s digital services.